EMEA 5mm Loose Lay Installation
Unite / Nordic 5.0 / Flow 5.0 LLT / Amalgam/ Eon / Loch / Inlet/ Cove
I. General Information
Shaw Contract luxury vinyl tiles (LVT) use the latest print film technology to replicate the aesthetics of natural looking products which have realistically occurring variations in colour, texture, sheen and gloss.
The installation of LVT is straightforward and follows the same BS 8203 guidelines that apply to all manufacturers of resilient floor finishes. It is important to note that the final appearance and durability of any floor covering is largely dependent on the quality of the subfloor that it is laid upon.
LVT can be installed upon a variety of substrates which have been suitably prepared.
The following instructions and recommendations should be followed for a satisfactory installation.
-
Acclimation of the material prior to its installation is required. All boxes of material should be removed from their delivery pallet and their contents emptied. The material should be stacked and stored not more than five boxes worth of material high within the laying area for at least 24 hours at an ambient temperature of between 18 °C and 27 °C and an ambient air Relative Humidity of not less than 40%.
-
Should the material have been stored or transported at temperatures less than 10 °C immediately prior to delivery, the conditioning time of the material should be extended to at least 48 hours. Note: Materials that have been transported or stored at temperatures that exceed 27 °C will also require a comparable conditioning time.
-
Install the product after all other trades have completed work that could damage the floor covering.
-
Use of cementitious patching, smoothing and levelling underlayment’s that meet or exceed maximum moisture level, pH requirements and compressive strength of 3,000 psi (20 N/mm squared) are more than acceptable.
-
Inspect all material for damage before installing. Claims will not be accepted for flooring that has been cut to size and/or installed.
If you have any concerns regarding the product fit or finish, please call Shaw Contract EMEA tel: +44 (0) 20 7961 4120.
II Subfloor Information
All subfloors must be clean, flat, dry and structurally sound. The correct preparation of the subfloor is a major part of a successful installation. Subfloor must be within a surface deviation of no greater than 5 mm under a 2 metre straight edge (Surface Regularity 2 (SR2) – BS 8203/BS 8204).
A. WOOD SUBFLOORS
-
Do not install material over wood subfloors that lay directly on concrete or over dimensional lumber or plywood used over concrete.
-
Basements and crawl spaces must be permanently dry. Where necessary, local regulations prevail.
-
All other subfloors - Plywood, OSB, particleboard, chipboard, wafer board, etc. must be structurally sound and be installed following their manufacturer’s recommendations. Local building codes, national standards and manufacturer’s recommendations may only establish minimum requirements of the flooring system and may not provide adequate rigidity and support for proper installation and performance. Plywood should be of a suitable flooring grade, be at least 6 mm thick and conform to all relevant country applicable regulations and standards.
-
The responsibility of determining if an existing flooring finish is suitable to be installed over rests solely with the installer/flooring contractor on site. If any doubts exist in relation to the suitability of such a base, serious considerations should be given to its full removal and its subsequent repair.
B. CONCRETE & SAND CEMENT SUBFLOORS
-
Floors shall be smooth, permanently dry, clean, and free all foreign material such as dust, wax, solvents, paint, grease, oils, and old adhesive residue. The surface must be hard and dense, and free from any substance to impede adhesion.
-
Cementitious based substrates should have a country applicable moisture vapor content that is deemed dry enough to lay resilient floor finishes upon. The ‘British Standard 8203’ requires surface hygrometer readings to have reached equilibrium and be below 75% Relative Humidity (RH). The ‘ASTM F1869’ states a maximum moisture level per the CaCl test method of 8 lbs. per 1000 ft2 in a 24 our period.
-
Do not install over cementitious bases with a history of high moisture or hydrostatic conditions. Excessive moisture in the subfloor could promote mold, mildew, and other moisture related issues like the trapping of moisture emissions under the flooring, which may contribute to an unhealthy indoor environment. Shaw Industries does not warrant nor is responsible for damage to floor covering due to moisture related issues.
-
pH level of concrete should be between 7-10.
-
The final responsibility for determining if the concrete is dry enough for installation of the flooring lies with the floor covering installer / flooring contractor on site.
NOTE: IT MAY NOT BE THE FLOOR COVERING INSTALLER'S RESPONSIBILITY TO CONDUCT THESE TESTS. IT IS, HOWEVER, THE FLOOR COVERING INSTALLER'S RESPONSIBILITY TO MAKE SURE THESE TESTS HAVE BEEN CONDUCTED, AND THAT THE RESULTS ARE ACCEPTABLE PRIOR TO INSTALLING THE FLOOR COVERING. WHEN MOISTURE TESTS ARE CONDUCTED, IT INDICATES THE CONDITIONS ONLY AT THE TIME OF THE TEST.
C. LIGHTWEIGHT CONCRETE & ANHYDRITE (GYPSUM) BASED SCREEDS
All recommendations and guarantees as to the suitability and performance of lightweight concrete and anhydrite (gypsum) based screeds under resilient flooring are the responsibility of the supplier / manufacturer. The installer of the system may be required to be authorized or certified by the manufacturer. Correct on-site mixing ratios and properly functioning pumping equipment are critical. To ensure proper mixture, slump testing is recommended.
-
Surface must be permanently dry, clean, smooth, free of all dust, and structurally sound.
-
As with all bases, Relative Humidity (RH) moisture tests should be conducted prior to undertaking any flooring works. Materials should have a country applicable moisture vapor content that are deemed dry enough to lay resilient floor finishes upon. The ‘British Standard 8203’ requires surface hygrometer readings to have reached equilibrium and be below 75% Relative Humidity (RH). The ‘ASTM F1869’ states a maximum moisture level per CaCl test method of 8 lbs. per 1000 ft2 in a 24-hour period.
-
The final responsibility for determining if the base is dry enough for installation of the flooring lies with the floor covering installer / flooring contractor on site.
-
Bond testing to determine compatibility of adhesive to the substrate is advised. Primer can be utilized to promote adhesion.
D. RADIANT UNDERFLOOR HEATING: WET / HYDRONIC ONLY
In most instance wet or Hydronic underfloor heating systems are installed below sand cement / Anhydrite screeds that have been laid to a depth somewhere between 50 to 75 mm thickness
It is imperative that has been previously commissioned and found to be fully functioning correctly prior to any part of the resilient floor coverings package being installed upon the bases surface. The underfloor heating system must be switched off for at least 48 hours prior to commencement of works and must remain off for a further 48 hours after the installation has been completed. It is also important to note that whilst the underfloor heating system has been decommissioned, an alternative heating source should be provided to ensure that the area of installation is kept at a constant temperature of between 18 °C and 27 °C.
After this 48-hour period, the underfloor heating system can be gradually recommissioned in accordance with standard industry recognized rules. Once operational, it is important to note that the heating system must not exceed the industry agreed maximum operating temperature of 27 °C at the underside of the floorcovering (the adhesive line).
In areas where the use of a higher temperature is unavoidable, agreement from your chosen adhesive manufacturer should also be obtained.
Failure to follow the aforementioned guidelines can result in floor finishes and their associated systems being irreversibly damaged.
E. EXISTING FLOOR COVERINGS
- Unite, Nordic and Flow can be installed over most existing hard-surface floor finishes, provided that the existing floor surface is fully adhered, clean, flat, permanently dry, structurally sound and free of any deflection. Existing sheet vinyl floors should not be heavily cushioned and not exceed more than one layer in thickness.
The responsibility of determining if an existing flooring finish is suitable to be installed upon rests solely with installer/ flooring contractor on site. If there is any doubt as to its suitability, the existing floor finish should be fully removed, and the base suitably repaired.
NOTE: Resilient floor finishes that require permanently bonding should
NOT be installed over existing floor finishes.
-
Installation of any floor finish is NOT allowed over any type of carpet.
-
Do NOT install over wood floors that are adhered to concrete.
-
Highly embossed ceramic tiles should be degreased and fully encapsulated with a suitable smoothing compound or levelling underlayment. Prior to undertaking such processes, always check with your chosen underlayment manufacturer for a suitable product recommendation.
-
Never use solvents or citrus adhesive removers to remove old adhesive residues. Mechanically remove or fully encapsulate as previously mentioned.
F. RAISED ACCESS PANEL SUBFLOORS
-
60 cm x 60 cm panels are recommended.
-
Raised access panels must be stable, level, flat, free and clean of existing adhesives.
-
Where / if necessary, repair or replace any loose or unstable panels.
-
Lippage (variation of height) between of panels must not exceed 0.75 mm gaps between panels must not exceed 1 mm.
-
There should be no deflection of the individual panels – Concave less than 0.75 mm.
-
The surface of the system must be flat and level within a surface deviation of no greater than 5 mm under a 2.0 metre straight edge.
-
Should access to the underside of the raised access base be a requirement, allow for framed inspection type hatches.
-
Use the appropriate installation methods for the product. Loose lay floor finishes that are being installed directly upon such panels must have their joint lines staggered so that they do not coincide with those found on the raised access system.
-
It is important to note that the joints of raised access bases can sometimes be physically viewed grinning back through the entire thickness of resilient floor finishes. Such disparity is not considered to be a product defect.
*NOTE: Should any doubt exist concerning the suitability of the raised access base, such surfaces can be covered with a 6 mm thick flooring grade plywood. Self-tapping screws, ring shank nails or divergent staples can be used to fix the boards. Should there be slight undulations or differences in height observed in the plywood sheets, a thin coat of a suitable flexible flooring / board grade feathering underlayment can be applied to the plywood’s facade prior to installing the floor finishes up on its surface.
III. Installation
INSTALLATION TOOLS
As with all trades, a skilled floor layer should have at their disposal a basic set of tools that should be clean and in good condition.
The following tools should be considered as part of the basic kit for the operations indicated.
Tape Measure, Chalk Line, Utility Knifes, T-Square, Adhesive Trowel (A1 or 1.5 mm x 5 mm ‘V’ notched trowel), Fluff Free Paint Roller, Broom or Vacuum and if necessary, tools for subfloor repair.
Recommended Adhesives are available from the following manufacturers:
F. Ball and Co, Mapei, Uzin, Thomsit, Tremco, Schonox, Bostik, Eurocol, Ardex or comparable subfloor treatment manufacturers.
Always follow adhesive manufactures application instructions
Note: Shaw Contract – 5.0mm luxury vinyl tiles have been designed to be installed wall to wall utilizing “pressure sensitive” type fixatives as bonding agents. Should the location be subject to temperature fluctuations that exceed 27 °C, 5.0mm thick luxury vinyl tiles should be fully bonded using a suitable high temperature grade LVT / PVC adhesive. Locations subject to rolling loads, casters chairs, high intensity foot traffic or are to be used in conjunction with suitable acoustic grade underlays should be bonded using similar fixatives.
INSTALLATION
On receipt of material, check that the colours correspond to those ordered and that the quantities are correct.
Inspect all planks for damage before installing. To minimize shade variation, mix and install planks from several cartons. Do not install similar looking planks or tiles next to one another.
Construction type expansion joints should not be overlaid with any part of a Shaw Contract system. The material should be stopped on either side of the joint and an expansion type cover strip should be incorporated into the installation.
5.0mm thick luxury vinyl planks and tiles can be installed in the following pattern like configurations.
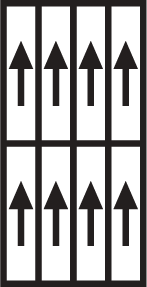 |
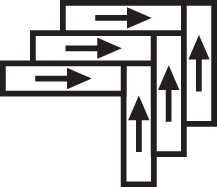 |
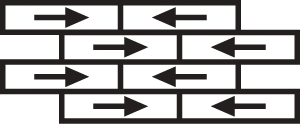 |
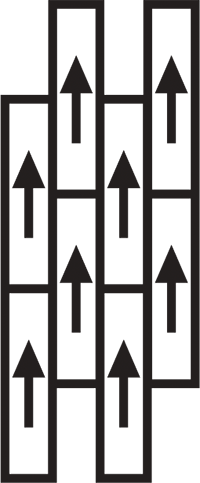 |
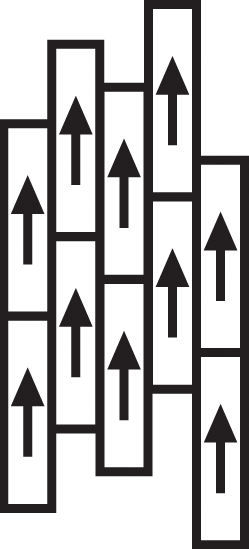 |
monolithic |
herringbone |
brick |
ashlar |
stagger |
-
Before laying out the floor, measure the room to find the optimum starting point that enables best use of the material and that minimizes waste. It is customary to centre rooms and passageways so that perimeter cuts are not less than half a tile in size.
-
The material should be run lengthwise adjacent to the longest wall, and if possible, parallel to incoming sunlight.
-
As with all tiled products it is best to work from markings made from a sprung chalk line.
-
The installation should be laid to ensure that all end of row cuts are a minimum of 16 cm’s in length.
-
Working out of multiple boxes at a time is recommended. To minimize shade variation, mix and install planks from several cartons. Do not install similar looking planks or tiles next to one another. Never mix different batches.
-
To properly cut LVT type systems, score the top side of the material with a utility knife. Bend the product and finish the cut through its reverse side. This will ensure the cleanest cut. Flooring grading LVT guillotines can also be used to perform this task.
- Roll the flooring immediately after installation with a 68 kg 3‐section flooring roller. Continue to roll the floor throughout the working day to ensure a proper bond is achieved and that no air is entrapped.
IV. Post Installation Care And Protection
-
To prevent damage, place plywood over the floor finish when heavy objects are being moved across its surface.
-
Place a non-staining floor protection over the installation to protect it when additional construction activity is to take place. Do not use plastic sheeting as it will trap moisture. Self-adhesive systems and tapes are not recommended as they can leave tacky residues which can attract dirt and spoil to the materials surface.
-
Protect all exposed edges by installing transition strips.
*NOTE: Should the aforementioned guidance leave any unanswered questions or require more clarity, please call Shaw Contract EMEA tel: +44 (0) 20 7961 4120